Water Jet Cutting Technology
Главная страница » Технология гидроабразивной резки
How does an water jet cutting machine work
The main principle of this equipment is the direction of a water stream at a high pressure to the cutting head, which supplies flow onto the working material through a small hole (called a “nozzle” or a “spout”). Cutting may be performed either with the use of water (water jet cutting), which is performed with no use of garnet, or with the use of a water-mixture. The former is used for shaping softer materials and the latter is intended for solid sheet materials.
Water jet cutting technology allows us to work with almost any kind of sheet material.
The most popular materials are metals which are the most widespread type of materials used in machine building. The water jet cutting of metals and other sheet materials allows for the fabrication of fashioned parts with high precision, which is very important for aircraft and machine building.
The advantages of water cutting
- Metal water jet cutting involves no thermal effect, so no waiting time is needed for for the metal to cool following cutting; induced cooling is also unnecessary. The temperature threshold in such a case is – 60-90 ºC.
- High efficiency of water jet cutting in shaping thick materials up to 180 mm.
- When using water jet cutting, no material burn-out or melting occurs at the cut edges, and furthermore no additional elements of alloys and steels burn out.
- The application of water jet cutting technology allows for simultaneous cutting of multiple material layers with no quality degradation, which allows for a high operating speed and conservation of consumables.
- The wide range of materials that are workable using water jet cutting include metals, marble, stone, porcelain, tiles, glass and many other materials.
- The lack of a fire or explosion hazard as well as the environmental friendliness of the process (no harmful gas emissions).
- Low tangential cutting force applied on the workpiece.
- Small cutting width, about 1 mm (a reduced amount of waste and an improved cost effectiveness of shaping materials).
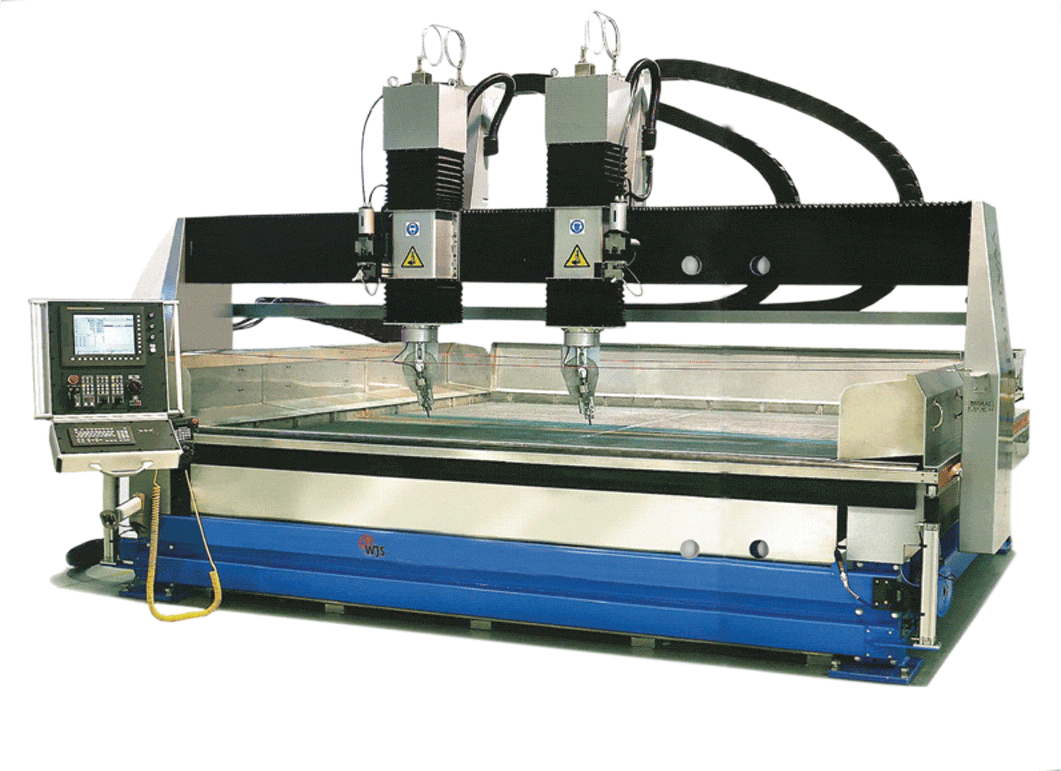